Cách đọc ký hiệu trên đá mài
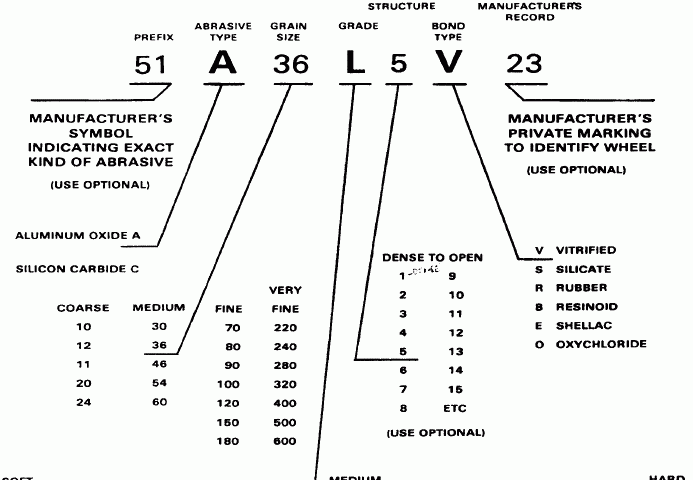
Phẩn lớn các đĩa mài chứa hạt mài bằng bột mài (coridon) (trắng, hổng) hay silicium cacbit (xanh,đen). Độ dẻo dai của hạt giảm với độ cứng tăng của hạt mài. Hạt mài cứng giòn lúc chịu tải nhỏ (mài tinh) có khả năng tự làm sắc qua hạt văng tách ra. Một độ dai đẩy đủ ở hạt chịu tải lớn (mài thô) ngăn chặn sự vỡ hạt sớm.
Hạt mài nên có độ cứng cao cũng như độ dai đủ và sức bền nhiệt.
Bảng 1: Các loại vật liệu mài | ||||
---|---|---|---|---|
Ký hiệu | Vật liệu mài | Độ cứng Knoop* N/mm2 | Độ bển nhiệt đến | Những lĩnh vực ứng dụng |
A | Coridon thường (Al203) | 18000 | Silicium cacbit (SiC) | Thép không hợp kim, thép không tôi cứng, thép đúc, gang dẻo) |
Coridon tinh khiết (Al203) | 21000 | Thép hợp kim cao và thép hợp kim thấp, thép tôi cứng, thép thấm than, thép dụng cụ, titan | ||
c | Silicium cacbit (SiC) | 24800 | 1370°c | Vật liệu cứng: hợp kim cứng, gang, thép gió, gốm, thủy tinh,vật liệu mềm: đổng, nhôm, chất dẻo |
CBN | Bor nitrít (BN) | 60000 | 1200°c | Thép gió, thép cán nóng và thép cán nguội |
D | Kim cương (C) | 70000 | 800°c | Hợp kim cứng, gang, thủy tinh, gốm, đá, kim loại không chứa sắt, không dành cho thép, liếc đĩa đá mài |
*Theo KOOP chiều sâu ăn vào được đo với một hình tháp bằng kim cương với góc mở 172,5°và 200°
Mài mòn ở hạt mài
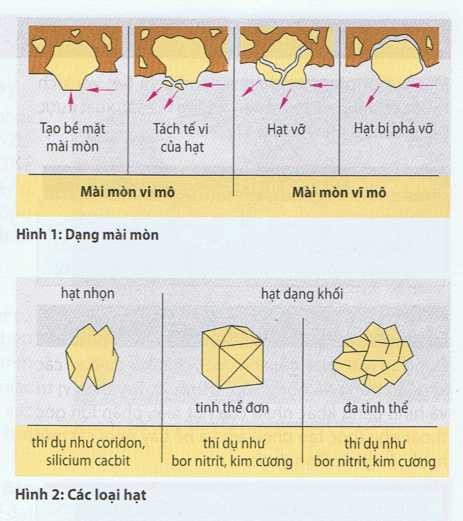
Lực cắt cao làm tăng trội việc đập vụn và sự phá vỡ của hạt khỏi sự kết dính, ở lực cắt nhỏ khi mòn ma sát nơi cạnh cắt tăng dần mới làm tải ở hạt cao đến nỗi làm các hạt nhỏ bị tách ra.
Qua việc tách ra và sự phá vỡ của hạt tạo thành cạnh cắt mới. Do vậy mà đá mài tự mài sắc.
Các loại hạt
Hạt nhọn phù hợp với vật liệu tạo phoi dài. Hạt dạng khối chống mài mòn ở vật liệu giòn. Hạt tinh thể đơn (một hạt tinh thể) có độ bền hạt cao, nó phù hợp để mài thủy tinh và gốm. Hạt đa tinh thể lúc mài kết thành nhiều hạt cắt nhỏ từ hạt qua sự tách vi tế (mikro) trước khi vỡ hoàn toàn. Các hạt do đó được dùng tốt hơn khi mài kim loại cứng.
Cỡ hạt
Số cỡ hạt tương ứng với sổ lỗ của rây trên chiều dài 1 inch, hạt nào đúng cỡ lọt qua thẳng xuống rây, trong khi một số hạt khác kẹt lại ở rây hẹp kê’ tiếp. Cỡ hạt thật mịn được tách ra bằng phương pháp lắng bùn. Cỡ hạt kim cương và hạt borit được xác định theo rây cỡ sàng bằng um. Cỡ hạt với ký hiệu D 150 (Hạt kim cương) cũng như B 150 (Hạt CBN) có độ lớn hạt trong khoảng từ 125nm và 150|xm.
Bảng 1: Độ cứng của bánh mài | ||||
---|---|---|---|---|
Cấp độ cứng | Ký hiệu | Khu vực ứng dụng | ||
A, B, C,D E,F,G | cực mém rất mém | Mài sâu và mài cạnh các vật liệu | ||
H, l,J,K L, M, N, 0 | trung bình mềm | Mài klm loại thông thường | ||
p, Q, R, s T, Ù, V, w X,Y,Z | cứng rất cứng cực cứng | Mài tròn ngoài, vật |
Sự kết dính của hạt mài
Bảng 2: Kết dính của bánh mài | ||
---|---|---|
Dấu hiệu | Loại kết dính | Lĩnh vực ứng dụng |
V | Két dính bằng góm | Mài phá và mài tinh thép với corundum (bột mài gốc oxit nhôm) và silic cacbua |
BBF | Kết dính với nhựa tổng hợp có sợi gia cường | Mài thô và mài cắt đứt, mài áp lực cao với corundum ãricon, mài định hình với kim cương và bor nitrua |
M | Kểt dính bằng kim loại | Mài định hình và mài dụng cụ với kim cương hay bor nitrua (mài ướt |
G | Kết dính bằng ma điên | Mài lỗ trong của kim loại cứng, thép gió, mài tay |
RF | Kết dính bằng cao su với sợi gia cường | Đĩa mài cắt Đĩa mài dẫn |
Sự kết dính có mục đích là giữ cho từng hạt chặt cứng với nhau đến khi nào cùn.
Đĩa mài kết dính bằng gốm có những buổng bọng và có thể dễ sửa liếc đá. Kết dính bằng nhựa tổng hợp giữ các hạt chặt hơn, do đó gây ra lực mài cao hơn.Tuy nhiên những hạt nhọn nằm tự do giúp mài mát hơn (ít nhiệt hơn).
Độ cứng của bánh mài
Bảng 1: Độ cứng của bánh mài | ||||
---|---|---|---|---|
Cấp độ cứng | Ký hiệu | Khu vực ứng dụng | ||
A, B, C,D E,F,G | cực mém rất mém | Mài sâu và mài cạnh các vật liệu | ||
H, l,J,K L, M, N, 0 | trung bình mềm | Mài klm loại thông thường | ||
p, Q, R, s T, Ù, V, w X,Y,Z | cứng rất cứng cực cứng | Mài tròn ngoài, vật |
Người ta hiểu độ cứng của đĩa mài không phải là độ cứng của hạt mài mà là khả năng đối kháng của sự kết dính chống lại sự phá vỡ hạt mài.
Trong phương pháp mài vật liệu cứng với mài mòn vì ma sát mạnh nhưng lực chịu tải của hạt nhỏ, ta chỉ có thể xác định chắc chấn “hiệu ứng tự tác động mài sắc” qua đĩa mài mềm. Mài vật liệu mềm đòi hỏi ở phoi dày môt lực giữ hạt iớn hơn, do đó đĩa mài cứng hơn.
Đĩa mài quá mểm luôn luôn không hiệu quả kinh tế vì độ mài mòn cao. Những hạt vỡ ra, trước khi bể mặt mài mòn hình thành. Đĩa mài bị mất hình dạng (prôfin) của nó,”vỡ toàn bộ”. Đĩa quá cứng thì ngược lại, nó giữchặt hạt rất lâu, trơn (chai) và bóng, đổng thời làm tăng áp lực mài và nhiệt độ ở vùng tiếp xúc. Độ cứng tác động của một đĩa mài trong quá trình gia công không chỉ tùy thuộc vào độ cứng mà còn ở cỡ hạt, khoảng trống (lỗ bọng xốp) và bề dày phoi (Hình 1).
Quy tắc làm việc
Ta chọn đĩa mài mém cho vật liệu cứng và đĩa mài cứng cho vật liệu mềm.
ở hạt mịn và phoi mỏng nên dùng đĩa mài mềm vì độ cứng tác động lớn hơn bởi qua đó các hạt này dễ vỡ hơn.
Tinh thể (cấu trúc)
Ta gọi tinh thể là quan hệ giữa hạt mài, chất kết dính và khoảng trống trong bánh mài (Hình 2). Các lỗ bọng cấu thành buổng chứa phoi và thúc đẩy sự làm mát khi mài. Các khoảng trống quá nhỏ sẽ làm tăng áp lực và nhiệt lúc mài.
Mã số của tinh thể càng lớn thì đĩa mài sẽ xốp hơn.
Các tinh thể phải thoáng hơn khi phoi trong vùng tiếp xúc phải được tiếp nhận vào trong các khoảng trống nhiều hơn.
Ký hiệu của hạt mài được trình bày theo thứ tự của sơ đổ dưới đây. Con số chỉ hình dạng có thể được thêm vào chữ hoa chỉ dạng (ngoài) biên (Bảng 2).
Cân bằng đĩa mài
Việc phân bổ hạt và chất kết dính không đễu ở đĩa mài không cân bằng làm hình thành các lực ly tâm. Việc cân bằng đĩa mài cực kỳ quan trọng ở đĩa mài lớn, bản rộng và đặc biệt với tốc độ chu vi cao. Để cân bằng tĩnh đĩa mài được để lên một cái cân để điểu chỉnh đúng hay một bợ đỡ lăn (giá đỡ lăn) (Hình 1).
Đối trọng cân bằng được di chuyển trong vòng rãnh, đến khi nào đĩa mài đứng yên ở mọi vị trí.
Liếc đá (Hình 2)
Liếc bánh mài có hai mục đích:
Sửa tiết diện (sửa prôíin) để tiết diện, các bán kính và kích thước đạt được trong vòng dung sai. Các đĩa mài mới kẹp cũng phải được chỉnh sửa độ đổng tâm và độ đảo mặt đẩu.
Mài sắc để mở rộng buổng chứa phoi qua việc loại bỏ các kết dính và đễ cải thiện sự tiếp xúc cắt của hạt mài.
Sau khi sửa tiết diện, đĩa mài bằng coridon và silicium cacbít được mài đủ sắc với dụng cụ liếc đá bằng kim cương hay thép (Hình3)
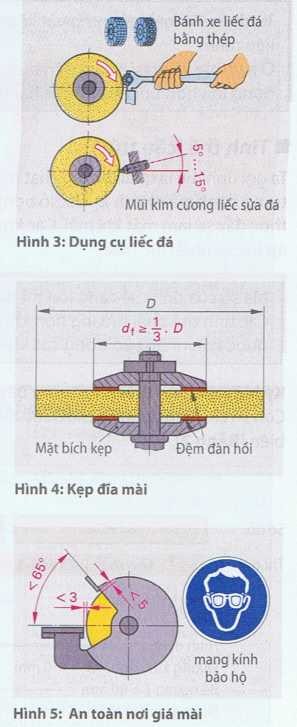
Đĩa mài kim cương hay đĩa mài CBN được sửa tiết diện với đĩa sửa đá bằng silicium cacbit hay bánh xe liếc tiết diện bằng kim cương. Khi làm sắc với đá liếc bằng coridon các chất kết dính được loại bỏ cho đến khi đạt được phẩn hạt nổi lên đạt mức tối ưu vào khoảng một phẩn ba của hạt.\
An toàn khi mài
Đá mài kết dính bằng gốm rất dễ vỡ. vét nứt nhỏ hay việc kẹp không đúng quy cách sẽ dẫn đến đá bị vỡ văng ra. ở tốc độ chu vi của đĩa bằng 80 m/giây (tương đương 288 km/giờ) các mảng vỡ văng bay ra trở thành nguy hiểm chết người. Chỉ khi nào giữ được quy tắc an toàn thì mài mới là một phương pháp gia công đáng tin cậy.
Quy tắc an toàn
Trước mỗi lần kẹp một đĩa mài bằng gốm phải thực hiện việc thửâm. Dùng ngón tay hay trục cho vào lỗ giữa đĩa mài giữ lại và dùng một thanh không phải kim loại gõ vào các vị trí khác nhau. Đĩa không có vết nứt sẽ cho tiếng kêu thanh.
Đĩa mài phải được đẩy vào trục nhẹ nhàng, không dùng lực mạnh để cưỡng ép.
Đường kính tối thiểu của mặt bích kẹp ở đĩa mài thẳng là 1/3. D, ở đĩa mài côn là 1/2 . D (Hình 4)
Để đảm bảo cho đĩa chạy phẳng tốt, chỉ được phép sử dụng mặt bích kẹp cùng cỡ, cùng hình dạng được tiện mặt sau với các đệm mềm, co giãn đúng kích thước.
Bánh mài với D > 80 mm sau khi lắp vào phải vượt qua thành công được việc chạy thử không tải ít nhất 5 phút với số vòng quay cao nhất cho phép trong vùng nguy hiểm được bảo đảm an toàn.
Chỉ được phép điểu chỉnh các bệ chi tiết hay nắp đậy bảo vệ khi máy ngừng (Hình 5).
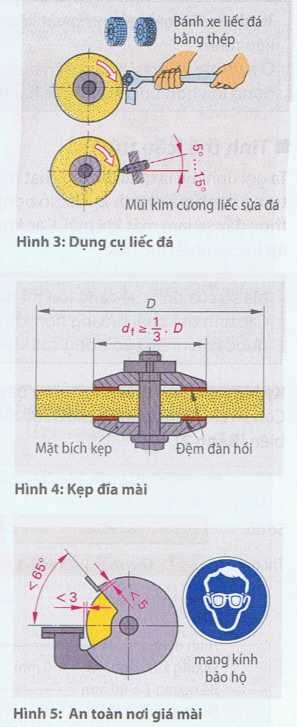
Lúc mài phải mang kính bảo hộ.3ệ6.6.3 Ảnh hưởng vào kết quả mài
Các yêu cầu về đặc tính chất iượng của chi tiết mài chỉ có thể đạt được, khi đĩa mài và điều kiện cắt của máy mài được điểu chỉnh cẩn thận trên chi tiết mài (Hình 1).
Thông số cắt gọt (Biến cắt gọt, độ lớn gia công)
Mỗi phương pháp mài được phân biệt qua chuyển động tiêu biểu và thông số cắt gọt (thông số điều chỉnh máy) (Hình 2 và Bảng 1).
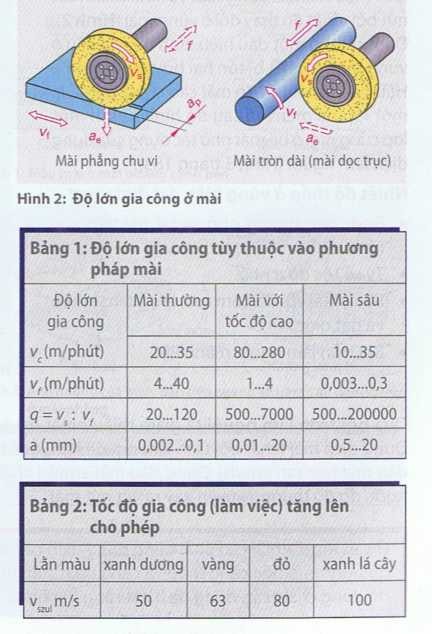
Tốc độ làm việc của đĩa mài V tương ứng với tốc
độ chu vi. Ngoài tốc độ làm việc cao nhất trên nhãn cũng có ghi số vòng quay cho phép.
Quy tắc an toàn
Trong mọi trường hợp tốc độ làm việc không được phép vượt quá tốc độ làm việc cao nhất ghi ở nhãn đĩa mài.
Đĩa mài và máy cho tốc độ làm việc gia tăng phải tuân thủ các quy định quốc gia về an toàn.
Thông thường tốc độ làm việc cao nhất khi mài lên tới 35m/giây trên những máy mài cố định. Tốc độ làm việc có thể tăng đến 160m/phút. Những đĩa mài này được đánh dấu bằng màu (Bảng 2).
Thí dụ: số vòng quay nào được điều chỉnh để một đĩa mài vối đường kính D =450mm cũng còn chạy với D= 250 m/phút ở tốc độ V, = 35m/giây.
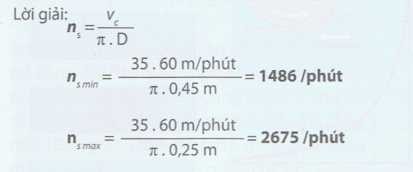
TỐC độ bước dẫn tiến vf (tốc độ phoi) tương ứng với tốc độ bước dẫn tiến bàn mài ở mài phẳng, ở mài tròn là tốc độ chu vi của chi tiết.
Bước dẫn tiến ngang f bằng mm cho mỗi hành trình cũng như bước dẫn tiến dài f bằng mm cho mỗi vòng quay ở mài tròn của chi tiết tùy thuộc theo bề ngang bs của đĩa mài.
Lượng ăn dao a (a ) là chiểu sâu cắt thẳng góc với chiểu dẫn tiến chính. Mài hoàn chỉnh không có lượng ăn dao gọi là “nẹt lửa” hay “có lửa
Người ta chọn lượng ăn dao lớn khi mài phá (mài thô), chọn lượng ăn dao nhỏ để mài tinh.
Thí dụ: Một trục thép được mài với một tốc độ làm việc là 35m/phút (q = 125). Vận tốc chu vi vf của trục là bao nhiêu?
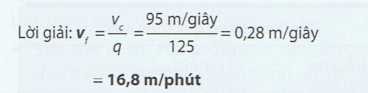
Sự tăng tốc độ dẫn tiến ở vận tốc làm việc không thay đổi làm tăng thêm sự mài mòn đĩa mài và độ nhấp nhô cũng như giảm nhiệt độ ở vùng biên.
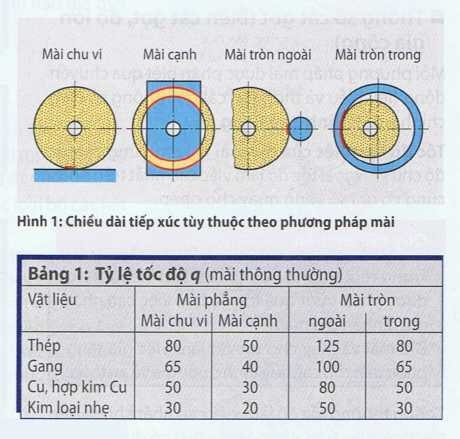
Nhiệt độ mài và làm nguội bôi trơn
Lúc mài phát sinh nhiểu nhiệt qua sự cọ sát của hạt mài lúc cấu thành phoi, ở vùng biên của phoi nhiệt có thể lên đến trên 1000°c. Nhiệt lúc mài là nguyên nhân làm tổn hại như kích thước sai lệch, ứng suất và hình thành vết nứt bởi nhiệt độ thay đổi ở vùng mài (Hình 2).
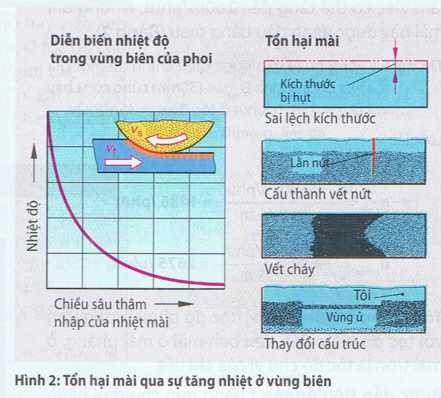
Đốm cháy là một dấu hiệu, tinh thể vật liệu ở vùng biên chi tiết bị tổn hại bởi sự quá nhiệt. Hậu quả của nhiệt độ mài cao cũng có thể là một lớp da mềm và sau đó hình thành một lớp cứng mới ở bể mặt nhờ tác dụng của dung dịch làm nguội (Hình 3 trang 183).
Nhiệt độ thấp ở vùng biên đạt được qua:
Bước tiến ngang nhỏ và bề dài tiếp xúc nhỏ.
Tỷ số tốc độ q nhỏ.
Bánh mài với độ bám cao, lựcgiữhạtthấp và hạt giòn.
Bôi trơn làm nguội mãnh liệt. Qua bôi trơn làm nguội ta giảm thiểu nhiệt ma sát, làm sạch buổng chứa phoi và làm nguội chi tiết. Dung dịch mài (chất bôi trơn làm nguội) hiệu quả nhất là dầu mài, nó làm giảm mạnh nhiệt ma sát hơn dầu mài hòa tan emulsi. Dùng dẩu mài emulsi khiến cho vùng biên nóng hơn và sau đó làm nguội đột ngột, do đó thường xuyên xảy ra vết nứt mài.
ở vận tốc đĩa mài cao phải dùng dung dịch cắt (dung dịch bôi trơn làm nguội) dưới áp suất cao. Tốc độ bước dẫn tiến càng thấp và càng phát sinh nhiều nhiệt hình thành thì lưu lượng dòng chảy (tốc độ dòng chảy) của dung dịch cắt càng lớn hơn.
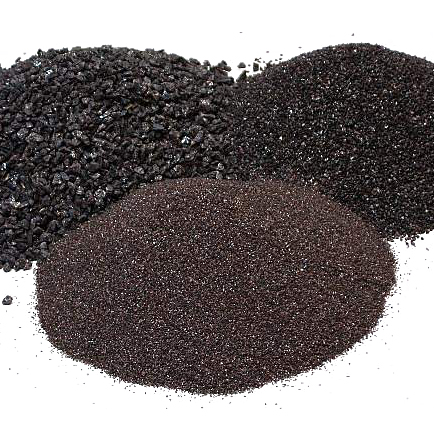
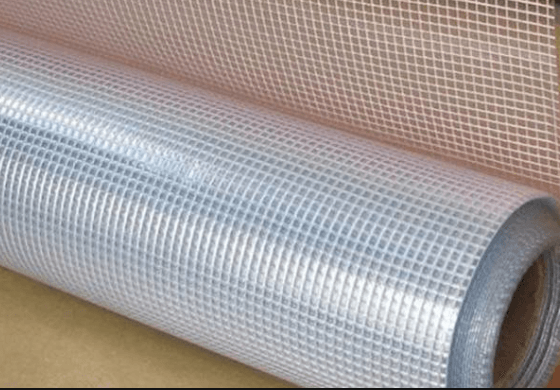